A Gating System is the assembly of channels which facilitates the entry of molten metal into the mold cavity.
Several common components of a gating system are the Pouring Basin/Cup, Down Gate/Downsprue/Sprue, Filtration Media, Runner, and Ingate/Gate.
Molten metal flows from the pouring basin or pouring cup down through the sprue, then passes through the runner and gates before entering into the mold cavity. Risers, (discussed in a separate article), are sometimes integrated into the gating system, and will typically be placed at the runner/gate junction. A riser, also known as a feeder, is a reservoir used to prevent cavities due to metal shrinkage as it cools.
There are several main classifications of Gating Systems correlated with the molding methods used throughout the foundry industry. Examples include Gravity-Fed, Bottom-Fed, and High Pressure. However, every foundry has unique methods and gating systems that are specific to their individual processes and alloys.
A Gating System Layout must be designed for every pattern that is manufactured. Just as the pattern creates the mold cavity that forms the casting, the Gating Layout creates the cavity within the mold that becomes the gating system. This Layout takes numerous factors into consideration and is tailored to the specific casting being poured. Either the foundry or pattern shop must design a Layout that exhibits the following characteristics:
- Completely fill the mold cavity.
- Fill the mold cavity with the least possible amount of turbulence.
- Prevent mold erosion.
- Establish proper temperature gradient in the casting.
- Promote directional solidification.
- Regulate the rate of flow of metal into the mold cavity.
- Prevent slag and non-metallic inclusions from entering the mold cavity.
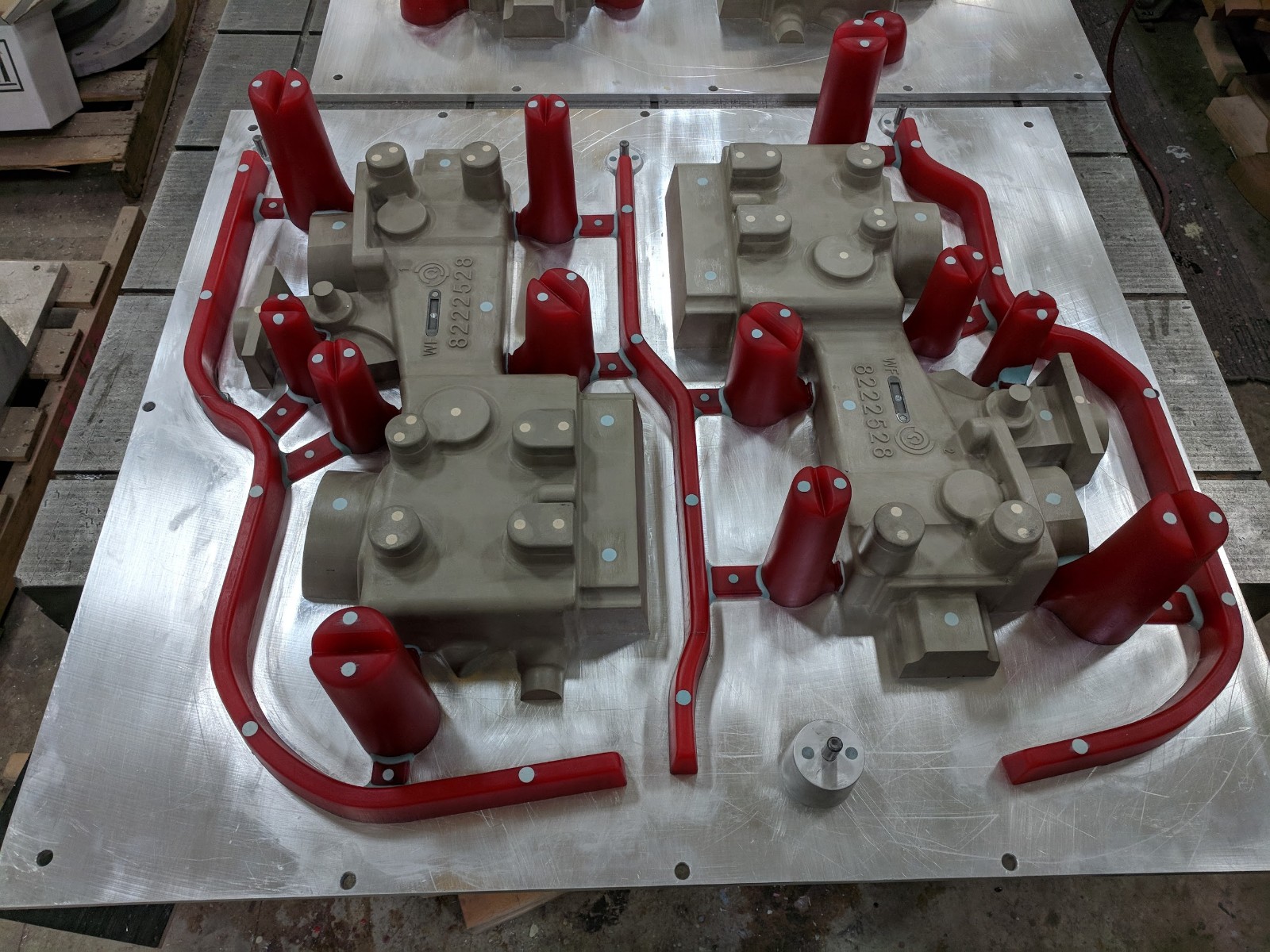
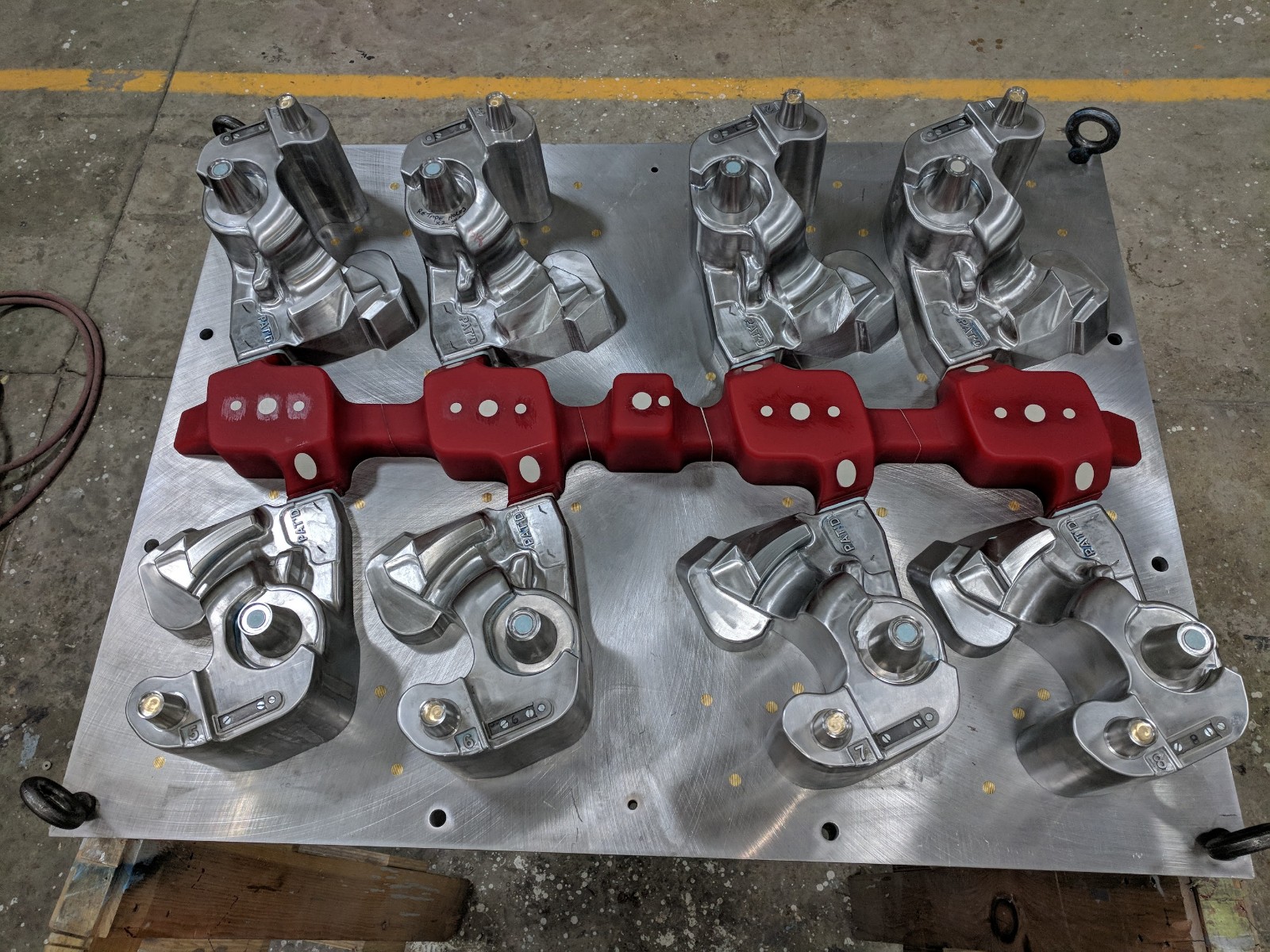
These pictures show a cope pattern (pictured right) and a drag pattern (pictured left) with Redboard gating.